

Providing the tank is fitted with wall baffles to eliminate gross swirl – there are usually four baffles, each with a width of about one tenth of the tank diameter – the overall flow fields sketched in Figure 1 develop. The popular, simple, robust and effective design with six blades mounted on a disc was adopted by Rushton as a standard for comparative tests. Paddle impellers with six flat blades are ancient.
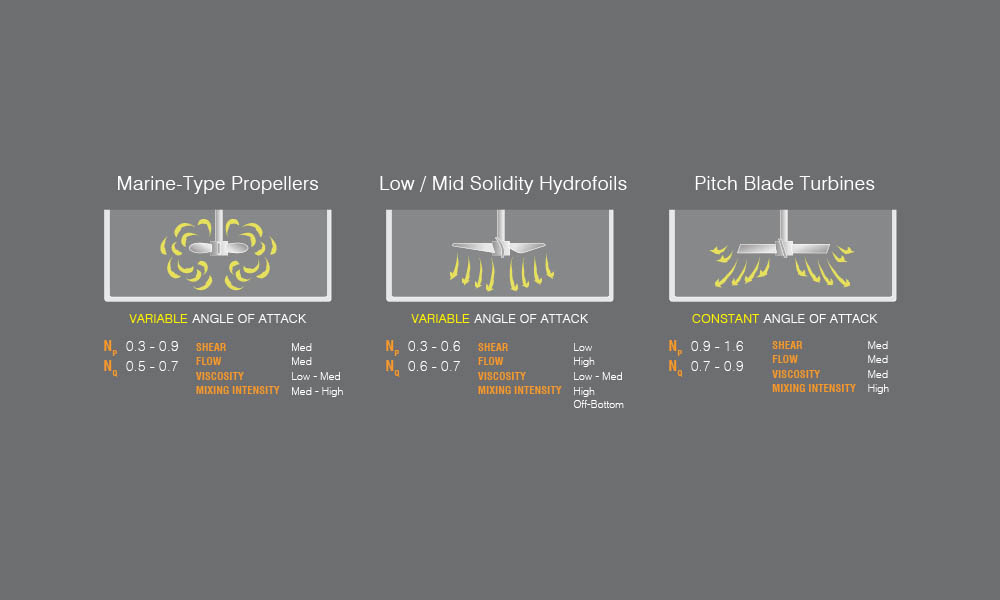
It is convenient to classify impellers as radial or axial pumping depending on the flow they generate in baffled tanks, Figure 1.įigure 3. Log-log plot of power number as a function of Reynolds number for Rushton, pitched blade and hydrofoil turbines. Low viscosity fluids can usually be mixed effectively in baffled tanks with relatively small high speed impellers generating turbulent flows, while high viscosity (typically above about 10 Pa s) and non-Newtonian materials require larger, slow moving agitators that work in the laminar or transitional flow regimes. For these reasons a wide variety of agitation devices have been developed.Ĭonventional, mechanically agitated, stirred tank reactors may be used for either batch or continuous processes, though the design and operating constraints are different in the two cases. Performance is crucially affected both by the nature of the fluids concerned and on how quickly the mixing or dispersion operation must be completed. Process requirements vary widely, some applications requiring homogenization at near molecular level while other objectives can be met as long as large scale convective flows sweep through the whole vessel volume. In addition to the particular ‘process results’ addressed above, on the basis of the present state-of-the-art, others mixing processes that might benefit from the use of up-pumping impellers are suggested.Agitation is the key to many heat and mass transfer operations that rely on mixing. Fourthly, they enable a significantly improved selectivity to be achieved in semi-batch reactors with competitive reactions when surface feeding is employed, similar to that obtainable with sub-surface feeding. Thirdly, whether wide or narrow blade, they can ingest floating solids at the lowest power input under unsparged conditions (and with less tendency for associated surface gassing), or when sparging is used. Secondly, they are the most effective impellers for foam breaking (SAFD) when placed close to the top surface of a fermentation broth.

Firstly, they can suspend solids in three-phase systems at much lower power inputs than Rushton turbines or other radial flow impellers, and at high gas flow rates, with less power and with much more stable flow, torque and power characteristics than with wide-blade, down-pumping hydrofoils. They are also very effective at other agitation-based processes. Also, with multiple impellers, the mixing time can be reduced by more than half compared with radial impellers. From the turbulent to the transitional flow regime, they handle larger quantities of gas without flooding, with a minimal loss of power and negligible torque and flow instabilities. Recently, this up-pumping concept has come of age, particularly with wide-blade, up-pumping hydrofoils that have the following advantages. In the early 1980s, reports appeared showing that, counter-intuitively, up-pumping impellers were very effective for gas dispersion.
